Ergonomic Studies
Why do we need ergonomic in a working environment?
Ergonomic is about designing for people and improving their working environments. This science of fitting a workplace to the user’s needs ensures that they are able to perform in a comfortable, conducive and safe working environment.
To design a critical facilities such as control room, it is mandatory to include ergonomic studies as part of the thought process during the design implementation. The goal is set to minimize human errors during operations. With the advancement of system automation, the expectations for the operator to retained their critical role is even higher. Without this thought process, the facility ultimately increases the risk of:
- Security / Privacy breach.
- Operating error in HMI (Human Machine Interface)
- Inability to carry out maintenance.
- Reduced hardware MTBF (Mean Time Between Failures)
- Reduced human efficiency.
- High operating expenses.
- Poor cognitive performance of operators.
- Movement congestion.
- Inability to perform during a crisis.
- Workplace safety and hazards.
- Health and Safety issues.
- High staff turnover rate.
- Inability to accommodate future upgrades.
The Design Principles
Datumstruct has setup a generic framework in their design process for critical facilities by applying requirements and recommendations related to the ergonomics of workplace and human factors engineering. ISO-11064 is the approach, which consist of evaluation of physical design and evaluations during the design process in terms of workstation and overview display functionality, to the overall design planning design of the project. To achieve the best results, there must be user participation as part of the design team, which forms part of the 9 design principles:
Principle 1: Application of human-centred design approach
Principle 2: Integrate ergonomics in engineering process
Principle 3: Improve design through iteration
Principle 4: Conduct situational analysis
Principle 5: Conduct task analysis
Principle 6: Design error-tolerant systems
Principle 7: Ensure user participation
Principle 8: Form an inter-disciplinary team
Principle 9: Document ergonomic design basis
There is no system or standards that can fully eliminate human errors. The goal of conducting such a comprehensive design program is to ensure that it is an error tolerant design.
The Design Team
User feedback is essential in project developments. It is crucial that we identify the previous design success and shortcomings in order to set design goals and operational objectives.
Setting up an inter-disciplinary design team or appointing user as part of the design team to oversee and influence all phases of the project development will be the priority. Actual combinations of disciplines included, may vary depending on the overall project scope, requirement and phases of design.
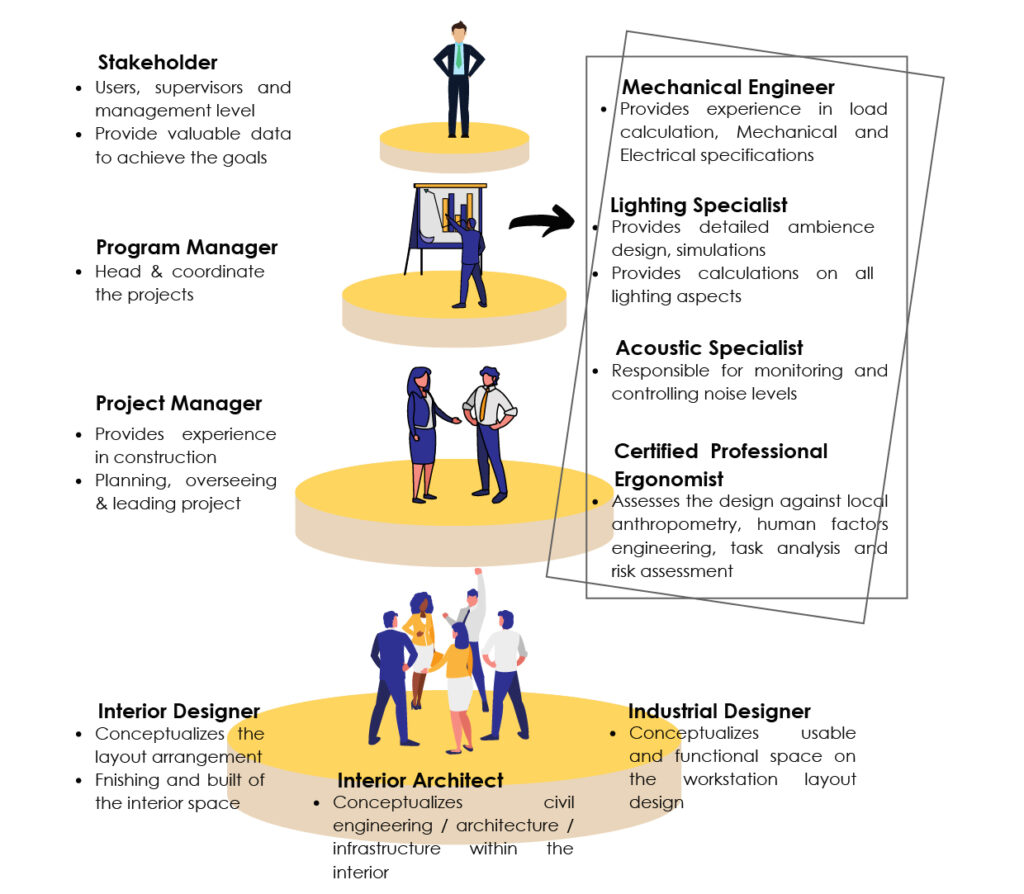
The Design Timeline
In order to achieve the design goal, it is important for the stakeholders to understand the process and progress of the design. A design timeline or project schedule must be submitted to objectively track and identify the required time to complete the individual task. With the schedule carefully crafted out, it will be understandable for the stake holder to permit sufficient time for the design team to carry out their task to avoid possible flaws or premature designs. If the task is carried out successfully, it will also means the financial allocations for the project is also safeguarded.
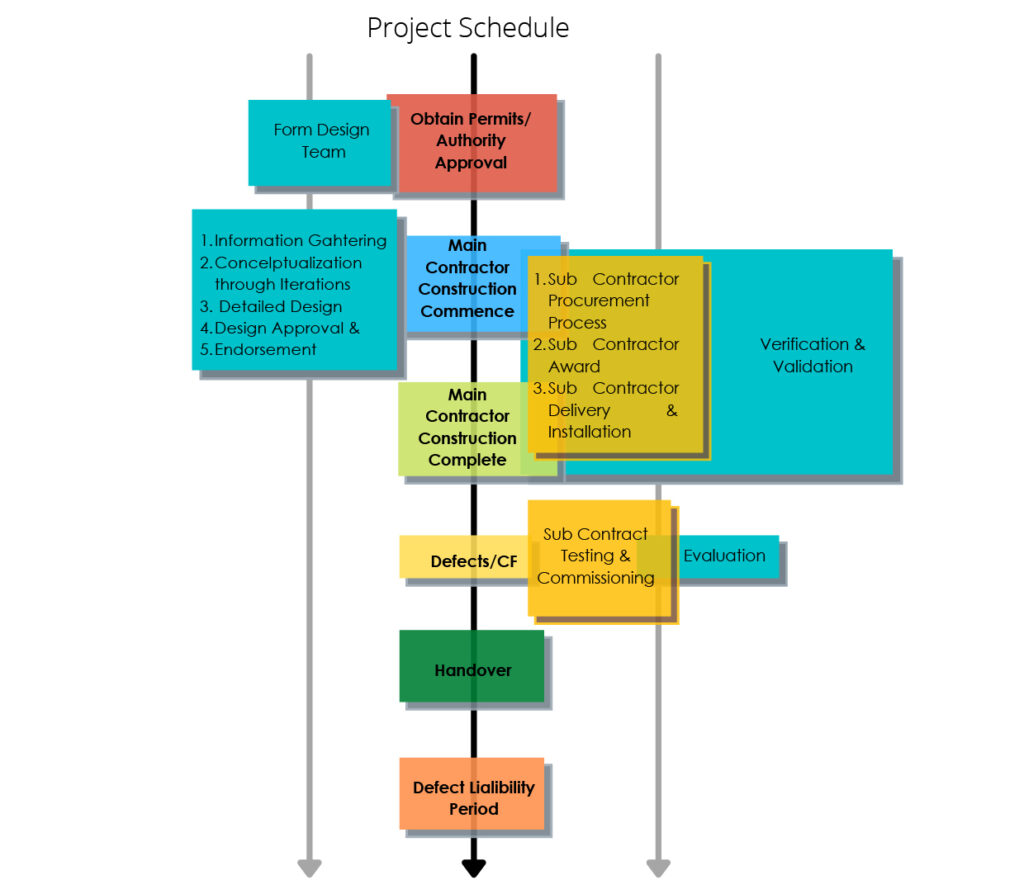
The Design Metholodgy
There are a total of 9 parts in the ISO 11064 design principles. The approach of this principal basically begins from the outside working its way inwards into more detailed design, as the team progresses inwards, the task would become more meticulous and extensive. The task should be planned in such way:-
- Identifying the space of the control center and assessing the surrounding architecture and orientation
- Floor plan zoning / layout – determining critical spaces surrounding the control room
- Control room layout – segregation of space, function, automation, etc.
- Workspace / workstation layout arrangement
- Visual Displays and HMI, Controls
- Environmental design (Interior Design / Lighting / M&E / HVAC)
The priority should focus on setting the control room space allocation follow-up by arrangement of the control room layout. The contents, namely the number of workstations, supervisors, equipment and wall display can determine what sort arrangement is best suited for its operation type. A typical sketch or draft layout plans can initiate discussions with the users to further improve and upgrade the design through iterations.
With today’s technology, the design phase and conceptualization through workshops and iterations, a series of design simulation via computer aided software allows for faster results and in-depth insights and visualization.
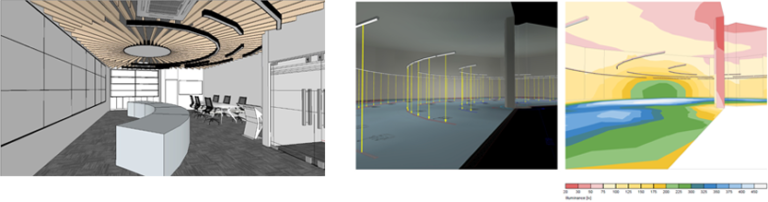
Despite the advancement of technology and software, ergonomics and human factor engineering is at times best evaluated and assessed with a physical mock up. This allows user to physically experience important first-hand measurements to aid the decision making process.

The final design process would be the detailing of visual aesthetics and technology integration of the rooms. We want to combine these different aspects through user experience by interior design and technology integration. Material selection process shall reflect a connection in visual and auditory human factors engineering to create a fulfilling user experience. The entire design process will be recorded in an assessment and progress report with the respective design plans, layouts, detailed design, 3D visuals, etc.
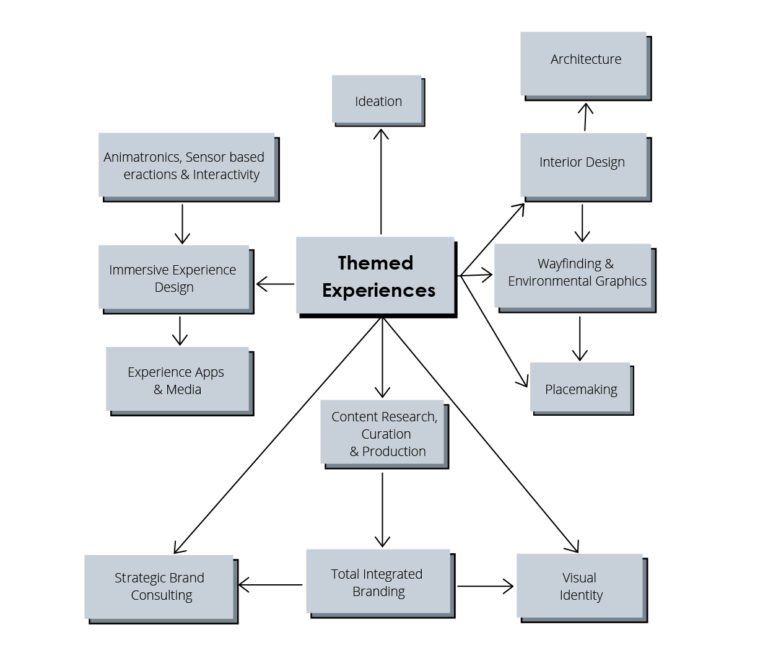
The Design Standards
In conjunction with the above context of principles and methods, the design is required to be adjusted to the industry’s international, local, organization and trade standards. Some of these standards could include:
- ISO 11064 Principals of design of Control Room
- ISO 6385 Ergonomic Principles in design of work systems
- ISO 9241 Ergonomics of Human System Interaction
- ISO 1503 Spatial Orientation and direction of movement
- ISO 8995 Lighting of work places
- Local anthropometry data sheet
- Local authority (Fire and safety, building council, DOSH)
- Stakeholder’s standards:
- Green building index
- Industry standards, e.g.
- Plantroom standards
- Civil Aviation Authority standards
- Related research white papers
PRODUCT
FEATURED CASES
WHAT’S NEW
- Redecon Consoles vs Office Furniture
- What Is the Difference Between an Air Purifier and Air Sanitizer?
- The New Norm In The Control Room During Covid-19 Pandemic
- MIRI Global Certified That Air Halo Portable Air Sanitizer Can Eliminate 99% of Covid-19 Virus
- We're Upgrading!
- REDECON Consoles Featured in Pengerang Integrated Complex (PIC)
©2021 Datumstruct CFS | All Rights Reserved